Tannery processing
Preparing hides begins by curing them with salt. Curing is employed to check the putrefaction of the protein substance (collagen) because of the chance of bacterial infection due to the time lag that might occur from procuring to processing. It removes the excess water from the hides and skins where water flows from inside because of the difference in osmotic pressure. Thus the moisture content of hides and skins gets greatly reduced. In wet-salting, the hides are first treated with carbonate and then pressed into packs for about 30 days. In brine-curing, the hides are agitated in a saltwater bath for about 16 hours. Generally speaking, methods employed for curing greatly make the chance of bacterial growth unfavorable; they also help to preserve the hides and skins at a very low temperature.
Tanning converts the protein of the rawhide or skin into a stable material, which will not putrefy and is suitable for a wide variety of purposes. Tanning materials form crosslinks in the collagen structure and stabilize it against the effects of acids, alkalis, heat, water, and the action of micro-organisms. The main types of tanning materials are :
Tanning can be performed with either vegetable or mineral methods; our partners exclusively employ vegetable procedures based on tannin (this is where the name tanning comes from). Tannin occurs naturally in the bark; the primary barks used in modern times are chestnut, oak, tanoak, hemlock, and mangrove. Hides are stretched on frames and immersed for several weeks in vats of increasing concentrations of tannin. Vegetable-tanned hides are flexible and can be used for luggage and furniture, among others for our seat covers and exclusive home accessories.
Depending on the finish desired, the hide may be waxed, rolled, lubricated, oiled, split, shaved and, of course, dyed. Suedes, nubucks, etc. are finished by raising the nap of the leather by rolling with a rough surface.
Leader in Tannery Sector
With the shifting of its facilities to the newly built Government “Leather Economic Zone” with Common effluent treatment plant (CETP), ATL has yet again created another benchmark in the tannery in the tannery sector. The new production unit has been built with the most modern and compliant factors into consideration. The new unit will not only improve efficiency in production but also increase inhouse production capacity by at least 20%.
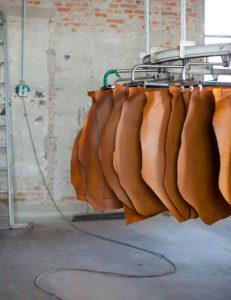
Taking Bangladesh to the World
Being the certified tannery of Bangladesh Apex Tannery is exporting in more than 20 countries including Italy, Hong Kong, China, Japan, India, Vietnam, Korea, the United States, etc. It has led to its presence in the global arena playing an attractive role in the major leather markets of the world.